The component carrier serves as a connecting element between a printed circuit board (PCB) and electronic components (such as LEDs, ICs, photo–diodes or sensors).
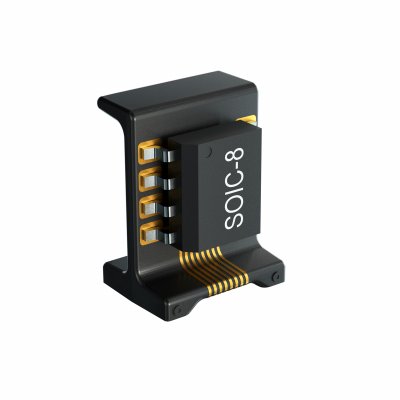
Component carriers are equipped with measuring sensors for detecting position
The measuring sensors of a scanning head for position detection, for example on a linear slide with guide rails, are often mounted onto flex PCBs. As magnetic, optical or inductive systems, they record the exact position of the slide. To do this the sensors must be positioned exactly at a 90 degree angle. The capability to mount these as precisely as possible improves the accuracy of the measurement results. A second sensor is often installed in the measuring head for redundancy. In addition, the status of the evaluation electronics is displayed using LEDs; these are mounted onto a flex PCB.

With HARTING’s component carrier the flexible PCB can be replaced completely. The injection-moulded plastic body already provides very precise 90-degree angles for mounting sensors. The component carrier eliminates the need for time-consuming manual assembly of the flex PCB. In addition, the sensors are positioned more precisely. Another advantage of the component carrier is that the width of the sensor modules can be further reduced to less than 8 mm.
The component carrier with the assembled electronic components, comes in a blister pack for further processing in SMD assembly facilities, and the soldered components are secured with an adhesive so that they cannot detach from their position while in the reflow oven. For more info visit: http://www.3d-mid.ch/
About HARTING 3D-MID
HARTING 3D-MID is offering the complete value chain for 3D-MID technologies from a single source, including development/prototyping of customer-specific products, injection moulding, laser direct structuring, metallisation, assembly and connection technology, as well as final inspection. Its core business is the production of mechatronic components for automobile manufacturing, industry, medical technology and sensor systems. HARTING is the largest supplier of 3D-MID components outside of Asia. HARTING 3D-MID is a business unit of the HARTING Technology Group, headquartered in Espelkamp, Germany.